What Is Prime Cost Definition Formula Calculation And Purpose
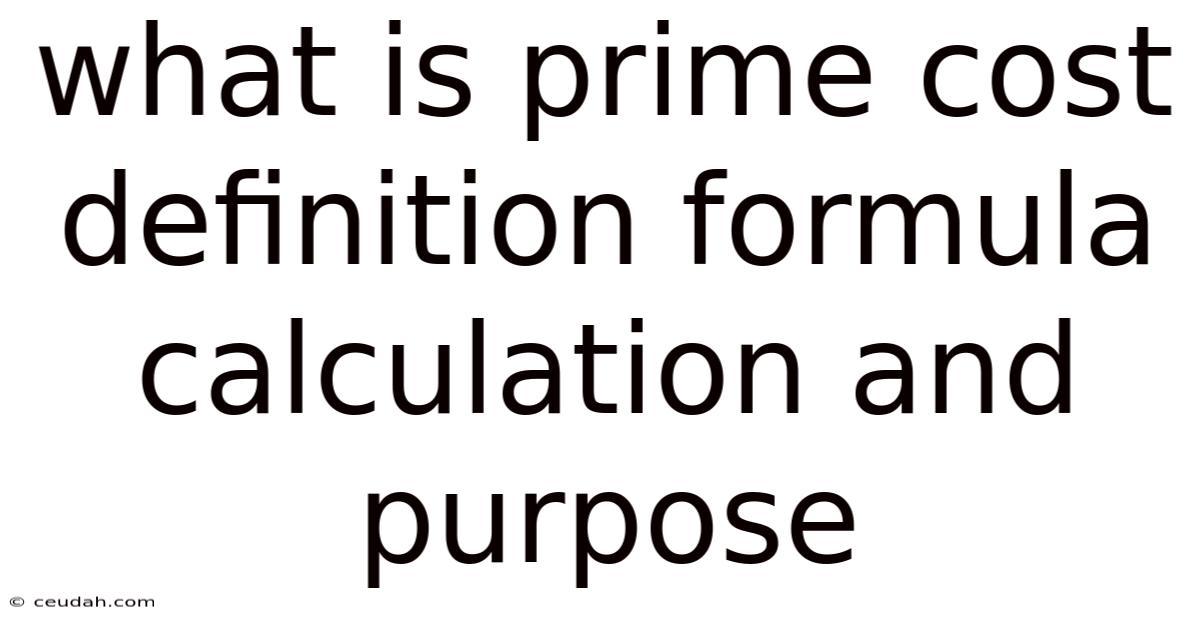
Discover more detailed and exciting information on our website. Click the link below to start your adventure: Visit Best Website meltwatermedia.ca. Don't miss out!
Table of Contents
What is Prime Cost? Definition, Formula, Calculation, and Purpose
What is the true significance of understanding prime cost in modern business operations?
Prime cost is a fundamental financial metric providing crucial insights into profitability and operational efficiency, empowering businesses to make informed strategic decisions.
Editor’s Note: This comprehensive guide to prime cost has been published today to provide readers with up-to-date information and practical applications of this vital business metric.
Why Prime Cost Matters
Prime cost is a crucial element in cost accounting. It provides a clear picture of the direct costs involved in producing goods or services. Understanding prime cost allows businesses to:
- Improve Profitability: By identifying and managing direct costs, businesses can optimize their pricing strategies and enhance their profit margins.
- Enhance Efficiency: Analyzing prime cost helps identify areas of operational inefficiency and waste, facilitating improvements in production processes and resource allocation.
- Make Informed Decisions: Accurate prime cost data supports strategic decision-making related to pricing, production volumes, and resource investment.
- Benchmark Performance: Comparing prime cost against industry benchmarks allows businesses to assess their competitiveness and identify areas for improvement.
- Better Cost Control: A detailed understanding of prime cost elements allows for better budgeting and cost control measures.
Overview of the Article
This article explores the key aspects of prime cost, including its definition, formula, calculation methods, and practical applications across various industries. Readers will gain a thorough understanding of why prime cost is important, how to calculate it accurately, and how to utilize this data for improved business performance. We will also explore the relationship between prime cost and other crucial cost accounting metrics.
Research and Effort Behind the Insights
The insights presented in this article are based on extensive research, incorporating established accounting principles, industry best practices, and real-world examples from diverse business sectors. The information is presented in a clear and concise manner to ensure accessibility and practical application.
Key Takeaways
Key Aspect | Description |
---|---|
Definition | The sum of direct materials and direct labor costs. |
Formula | Prime Cost = Direct Materials Cost + Direct Labor Cost |
Calculation | Requires accurate tracking of materials and labor costs directly attributable to production. |
Purpose | To understand the core costs of production and improve profitability and efficiency. |
Applications | Pricing strategies, cost control, performance benchmarking, and strategic decision-making. |
Let’s dive deeper into the key aspects of prime cost, starting with its foundational principles and real-world applications.
Exploring the Key Aspects of Prime Cost
-
Definition of Prime Cost: Prime cost represents the sum of all direct costs incurred in the production process. This excludes indirect costs such as factory overhead, administrative expenses, and selling and distribution costs. The two primary components are:
-
Direct Materials Cost: This includes the cost of all raw materials, components, and supplies directly used in the manufacturing process. It encompasses the actual cost of the materials plus any freight or import duties. Accurate inventory management is crucial for precise calculation of direct materials cost.
-
Direct Labor Cost: This encompasses the wages, salaries, and employee benefits directly related to the production of goods or services. This excludes salaries of administrative staff or sales personnel. Accurate timekeeping and payroll records are essential for accurate calculation.
-
-
Formula and Calculation of Prime Cost: The formula for calculating prime cost is straightforward:
Prime Cost = Direct Materials Cost + Direct Labor Cost
For example, if a company spends $10,000 on direct materials and $5,000 on direct labor in a given period, the prime cost would be $15,000. The accuracy of this calculation heavily relies on the accuracy of the data used for direct materials and direct labor.
-
Practical Applications of Prime Cost: Understanding prime cost offers several practical applications in business:
-
Cost-Plus Pricing: Many companies use prime cost as a base for setting prices. They add a predetermined markup percentage to the prime cost to cover overhead and desired profit margins. This method ensures that prices cover at least the direct costs of production.
-
Budgeting and Cost Control: By tracking prime cost over time, businesses can identify trends, variances, and potential areas of cost savings. This allows for better budgeting and more effective resource allocation. Regular analysis helps in identifying inefficiencies in material usage or labor productivity.
-
Performance Evaluation: Prime cost can be compared against budgeted prime cost to assess the efficiency of production processes. Significant variances may indicate the need for process improvements or investigation into cost drivers.
-
Decision-Making: Understanding prime cost is crucial for making informed decisions related to product pricing, production volume, outsourcing, and investment in new equipment or technologies. A decrease in prime cost, keeping quality constant, can be a significant competitive advantage.
-
-
Limitations of Prime Cost: While prime cost provides valuable insights, it's essential to acknowledge its limitations. It doesn't capture all costs associated with production. Overhead costs, which are indirect and often significant, are excluded. This means prime cost alone cannot provide a complete picture of total production costs.
-
Prime Cost vs. Conversion Cost: It’s crucial to distinguish prime cost from conversion cost. Conversion cost represents the cost of converting raw materials into finished goods. It includes direct labor and manufacturing overhead. Therefore, conversion cost includes elements not found in prime cost.
-
Prime Cost and Profitability Analysis: By analyzing prime cost alongside other cost categories, businesses can perform comprehensive profitability analysis. Comparing prime cost to revenue provides valuable insights into the efficiency of production and pricing strategies.
Closing Insights
Prime cost, a simple yet powerful metric, is essential for effective cost management and strategic decision-making. Its application in cost-plus pricing, budgeting, performance evaluation, and strategic planning allows businesses to optimize operations, improve profitability, and gain a competitive edge. While it doesn't reflect all production costs, its use alongside other cost accounting metrics provides a comprehensive view of business performance. Understanding and consistently monitoring prime cost is vital for long-term business success.
Exploring the Connection Between Inventory Management and Prime Cost
Effective inventory management is intrinsically linked to accurate prime cost calculation. Inefficient inventory practices can lead to inflated direct materials costs and skewed prime cost figures. Poor inventory control can result in:
- Obsolescence and Spoilage: Outdated or damaged materials increase direct materials costs and reduce prime cost accuracy.
- Stockouts: Lack of materials can halt production, leading to lost revenue and inaccurate direct labor cost calculations.
- Excess Inventory: Holding excessive inventory ties up capital and increases storage costs, indirectly influencing prime cost analysis.
Further Analysis of Inventory Management
Aspect | Impact on Prime Cost | Mitigation Strategy |
---|---|---|
Poor forecasting | Inaccurate material purchasing, leading to overstocking or shortages. | Implement robust forecasting techniques using historical data and market trends. |
Inefficient storage | Increased storage costs and potential material damage. | Optimize warehouse layout and utilize appropriate storage solutions. |
Lack of tracking | Difficulty in tracking material usage and identifying waste. | Implement barcoding or RFID tracking systems. |
Obsolete materials | Increased write-offs and inflated direct material costs. | Regular inventory reviews and strategic disposal of outdated stock. |
FAQ Section
-
What is the difference between prime cost and total cost? Prime cost only includes direct materials and direct labor, while total cost includes all costs—direct and indirect—associated with production.
-
Can service businesses use prime cost? Yes, but the components will be different. Direct labor will be a major component, while direct materials might be minimal or non-existent (e.g., consulting services).
-
How frequently should prime cost be calculated? The frequency depends on the business's needs, but monthly or quarterly calculations are common for regular monitoring and analysis.
-
What are some common errors in calculating prime cost? Inaccurate inventory tracking, incorrect allocation of direct labor costs, and overlooking minor direct material costs are common errors.
-
How does prime cost help in pricing decisions? It serves as a foundation for cost-plus pricing, ensuring prices cover at least the direct costs of production, leaving room for overhead and profit.
-
How can technology improve prime cost calculation accuracy? ERP systems, inventory management software, and time-tracking applications can significantly improve data accuracy and streamline the calculation process.
Practical Tips
- Implement a robust inventory management system: Track materials accurately from purchase to usage.
- Maintain detailed records of direct labor: Accurately track employee time spent on production activities.
- Regularly reconcile inventory and cost records: Ensure data consistency and identify any discrepancies promptly.
- Use technology to automate data entry and calculations: Streamline processes and minimize manual errors.
- Analyze prime cost trends over time: Identify patterns, cost drivers, and areas for improvement.
- Benchmark prime cost against industry standards: Assess competitiveness and identify areas needing optimization.
- Regularly review and update cost accounting procedures: Ensure accuracy and relevance to changing business conditions.
- Collaborate with employees involved in production: Gather insights to improve accuracy and efficiency.
Final Conclusion
Prime cost, while a simple concept, offers profound insights into a business's operational efficiency and profitability. By understanding its definition, formula, and applications, businesses can make informed decisions about pricing, production, and resource allocation. Consistent monitoring and accurate calculation of prime cost are critical for sustained success in today’s competitive business environment. Investing time and resources in developing efficient cost accounting processes ensures the effective use of this valuable business metric. A thorough understanding of prime cost empowers businesses to optimize their operations and achieve greater profitability.
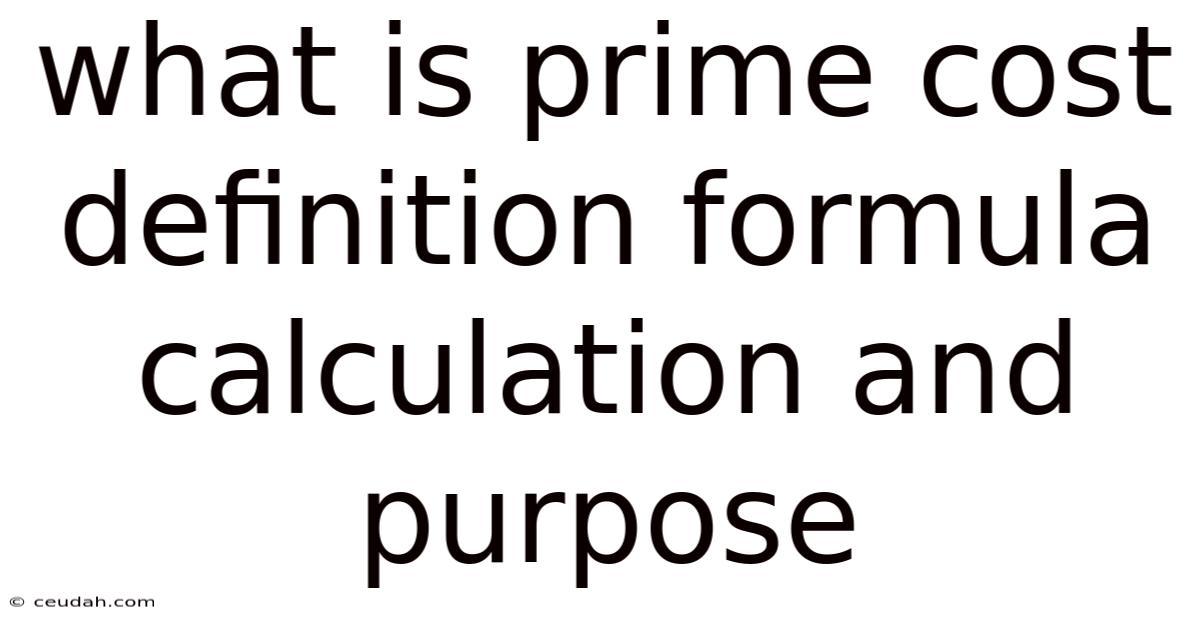
Thank you for visiting our website wich cover about What Is Prime Cost Definition Formula Calculation And Purpose. We hope the information provided has been useful to you. Feel free to contact us if you have any questions or need further assistance. See you next time and dont miss to bookmark.
Also read the following articles
Article Title | Date |
---|---|
Prepayment Privilege Definition | Apr 15, 2025 |
Pull Through Production Definition | Apr 15, 2025 |
Prize Indemnity Insurance Definition | Apr 15, 2025 |
What Does Provisional Credit Mean | Apr 15, 2025 |
Protected Fund Definition | Apr 15, 2025 |